Fjell Fishmeal plants & Fish oil processing
Fish oil factory - Fishmeal factory - Fishmeal factory equipment
Fish meal and fish oil see high value and high demand in the market
We deliver processing plants and process equipment for production of high-quality fishmeal and fish oil from bycatch, small pelagic species, and off-cuts from slaughterhouses and processing plants
We deliver significant savings in operating costs and improve the environment profile by
- World-class equipment in each process step
- Optimised plant design, incl. compact and modular design
- Optimizing energy recovery between process steps and by means of site integration
Our patented Energy saving solution for fishmeal and fish oil processing provides excellence in steam heat recovery and energy efficiency - resulting in as low as 186 kWh energy input per tonne raw material.
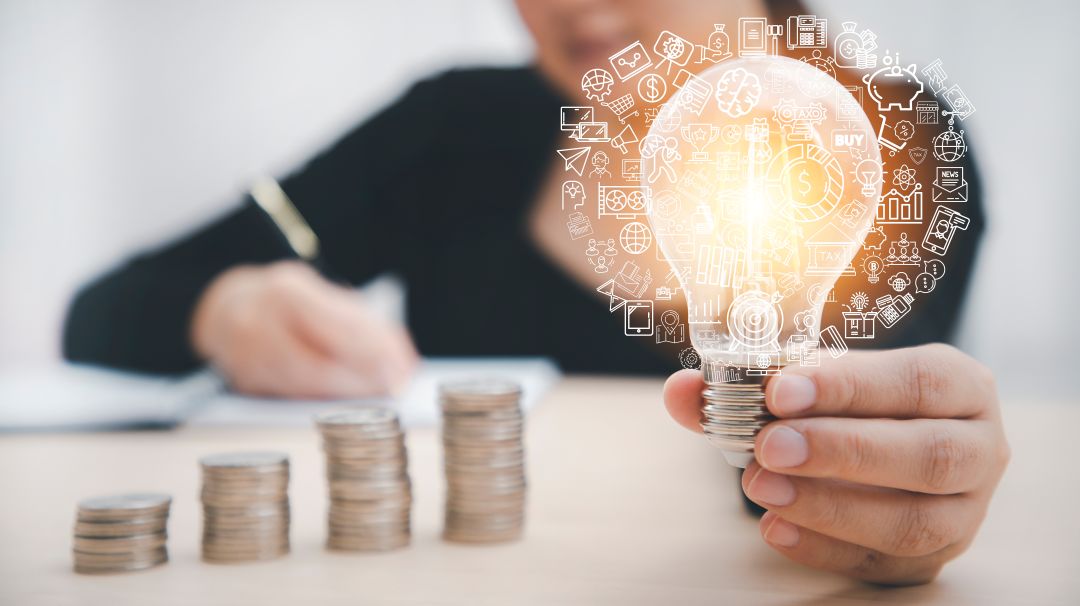
Proven solution - Profitability and low energy consumption
Cooking - Pressing - Decanter and separators - (MVR) Evaporator - Drying
Fjell Technology Group can deliver turnkey solutions for complete fishmeal & fish oil plants. Our fishmeal plants can include fishmeal factory equipment such as:
- Pre-heating & Cooking in Fjell steam heated screw cookers
- Pressing in Twin screw press
- Separation in decanters and separators incl. polishers for oil separation. Or alternatively 3-phase separation in tricanter incl. oil polisher
- Evaporation of stick water in waste heat or MVR evaporator
- Drying of press cake, decanter solids and concentrate in Fjell Turbo disc dryer before milling and cooling of meal. The Fjell Turbo Disc dryer is a patented solution with improved durability and higher performance than traditional disc dryers.
- Energy optimized factory by patented design - target theoretical 186 kWh/tonne energy consumption per tonne raw material
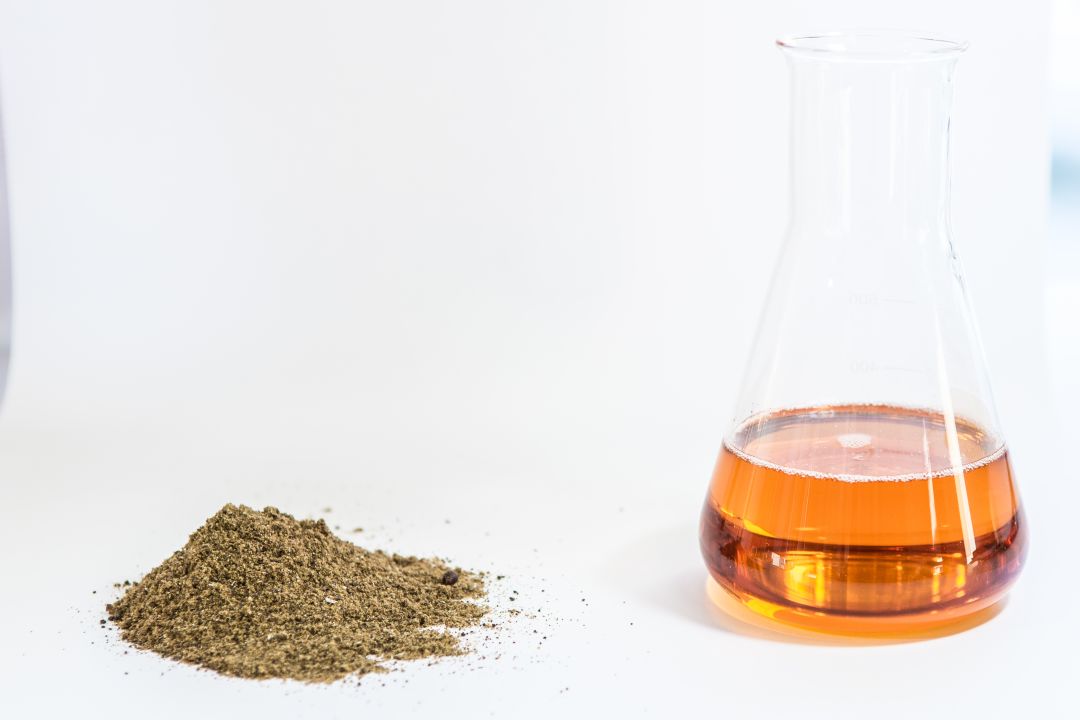
Meet our Fishmeal Dryer
- The Fjell Turbo Disc (TD) Dryer is the corner stone of the fishmeal & fish oil plant.
- Unique patented drying technology – no stay bolts and with optimized design for first-class performance giving high product quality.
- Risk for SCC (Stress Corrosion Cracking) is eliminated as welds are not exposed to the process.
- Risk for steam leakage is eliminated as welds do not seal between pressurized and non-pressurized side.
- Improved lateral bending strength of discs with patented claws design that act as reinforcement beams in radial direction. This reduces the risk for stress corrosion cracking in foot welds between the discs.
- Smooth disc surface secures efficient self-cleaning and maximises heat transfer.
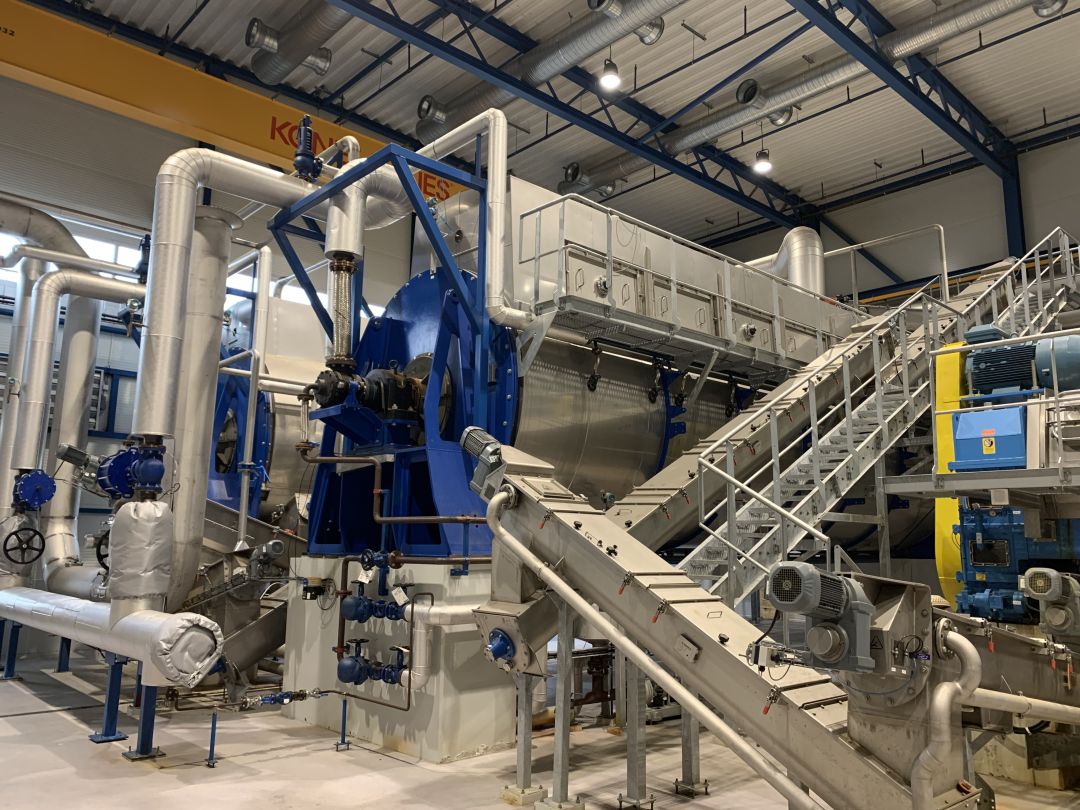
Meet our Screw Cookers
Fjell designs several versions of Preheaters, Single stage screw cooker, and Double stage screw cooker.
- We deliver all the classic sizes of Stord SS type cookers from small units for a few MT raw material per hour to the larger SS160/14 rated for 50 MT per hour.
- The standard cooker SS uses steam as heating medium. Optionally, Fjell can design cookers that reuses the energy and uses hot water as heating medium.
Our two stage process improves
- Process control
- Oil yield from marine and animal raw material
- Energy efficiency - as first stage uses waste heat and second stage low pressure steam
- Process performance as stick water, and suspended solids content is reduced.
Our cookers are manufactured with a steam heated (up to 10 bar) rotor with hollow flights. The rotor is placed inside a stator with steam jacket. Indirect heat is gently applied to the residual giving full coagulation control and efficiency.
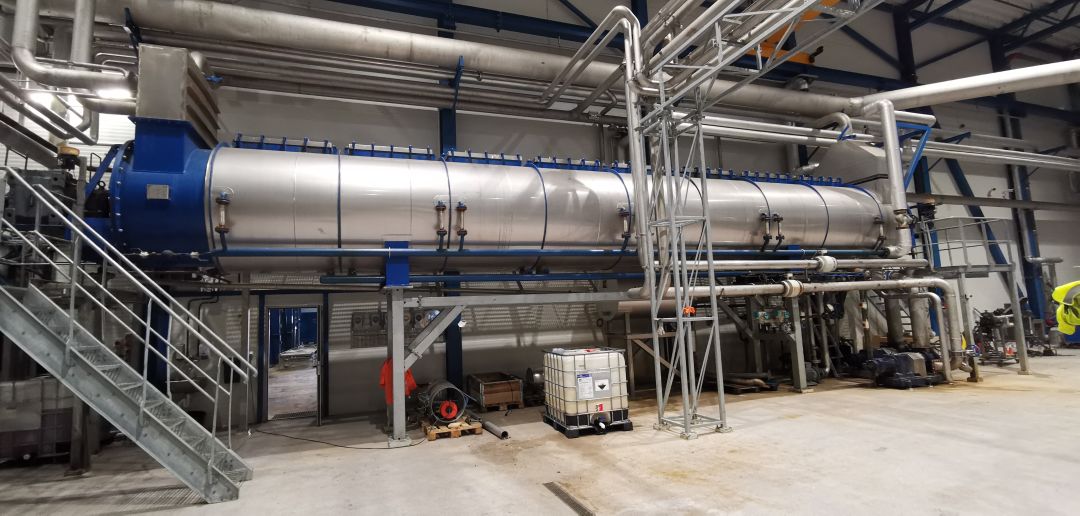
Your design and EPC specialist for Fishmeal and Fish oil plants
We offer end-to-end solutions for fishmeal and fish oil plants and provide full Design, Engineering, Procurement and Construction (EPC) capability to your project.
Our design and engineering team is ready to support you with process designs:
- Heat and mass balance scheme and process optimisation to your performance targets
- Process flowsheets
- 3D drawings where compactness and modular designs can be met if needed
- P&ID
- Fully automated plant and PLC system design
Our projects and solutions
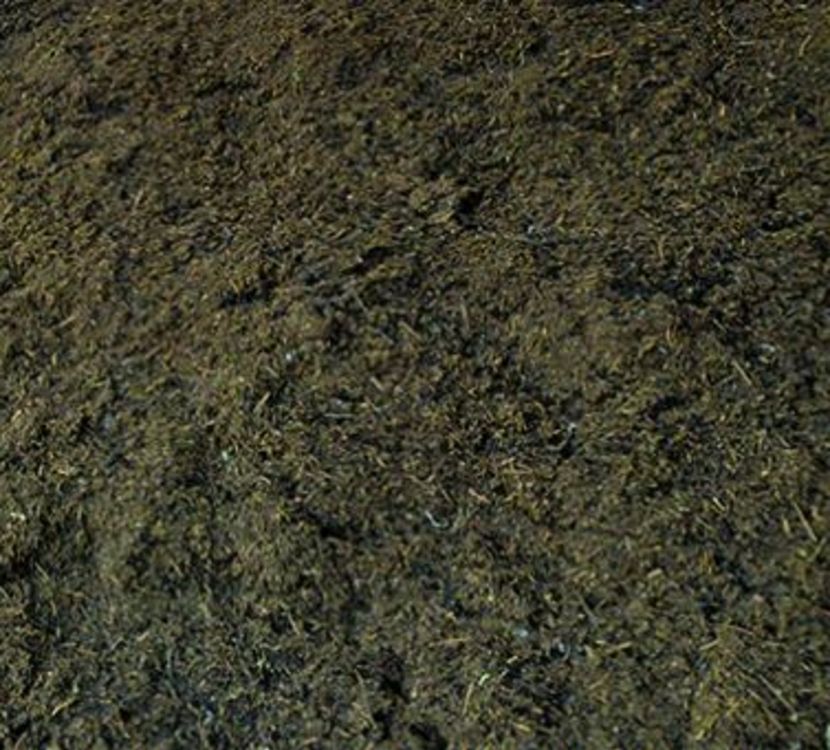
Biogas Digestate Drying Systems
Fjell Technology Group offers energy efficient biogas digestate drying systems. High performance and long-lasting durability!
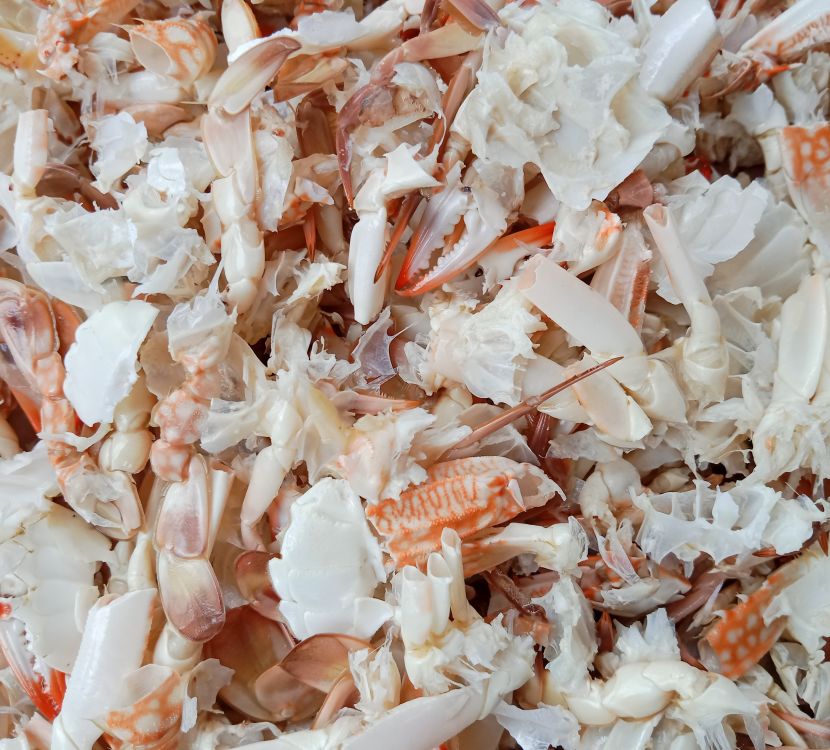
Processing of other rest raw materials
Fjell Technology Group has a unique portfolio of dewatering & drying technology that enables us to dry up almost all types of raw material.
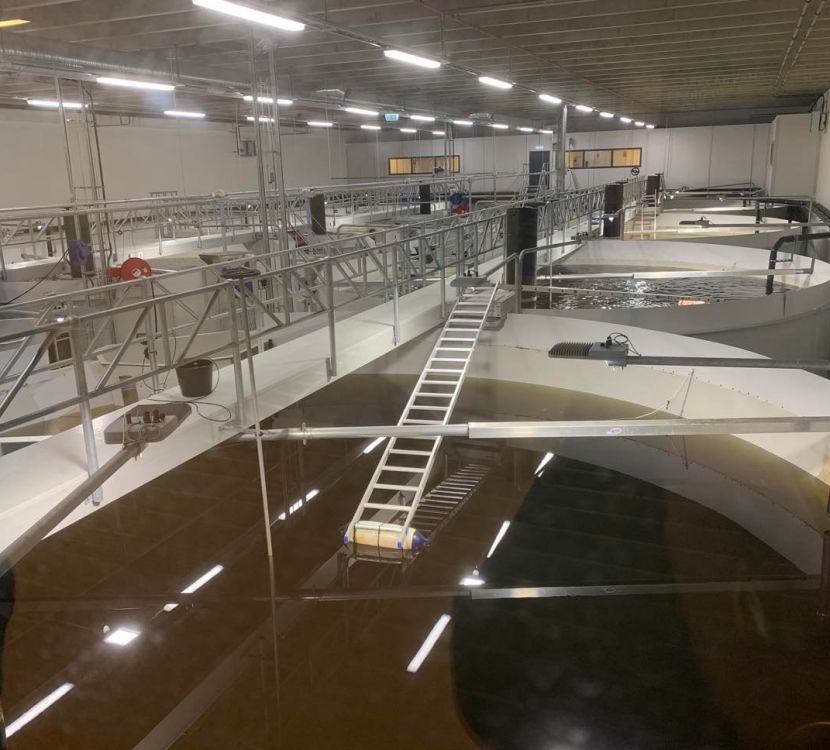
FRS Wastewater treatment systems.
Fjell Technology Group offer different high-quality wastewater treatment solutions customised to the customer's needs in all regards.
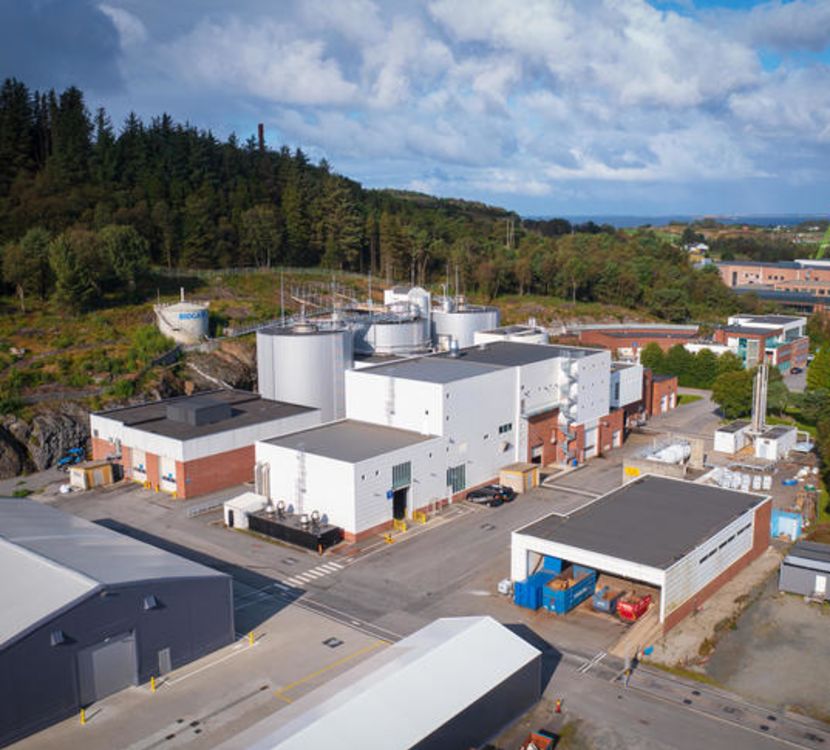
Municipal waste water treatment and Digestate Drying
We deliver world class sludge dryer systems for Municipal waste water treatment or digestate. Our patented energy saving solutions can reduce energy consumption with up to 40% compared to conventional…
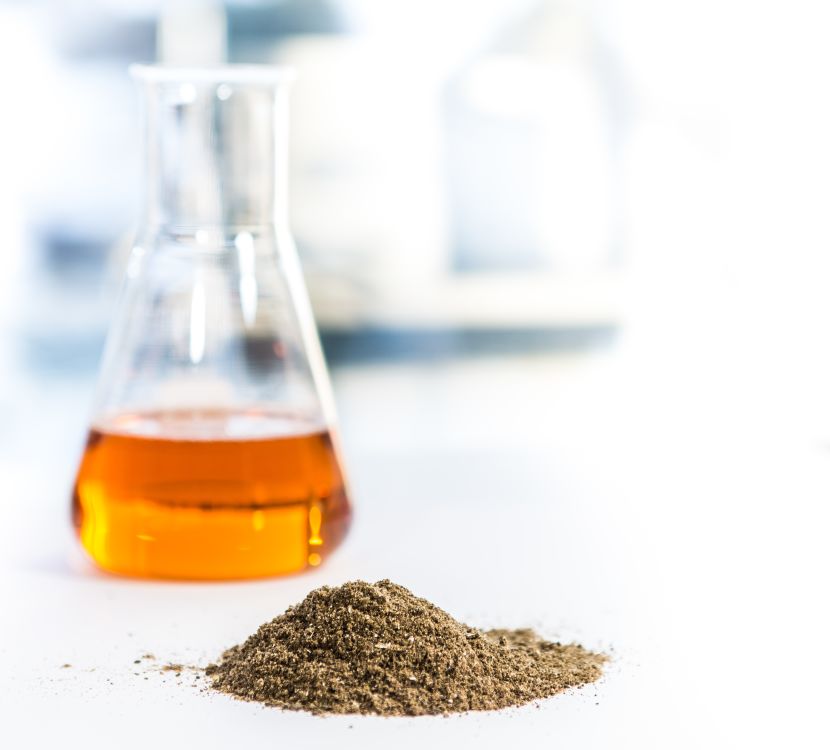
Fjell Fishmeal & fish oil plant
Fjell combines world class equipment and competence, with patented energy saving solutions. We can achieve up to saving up to 40% energy compared to modern conventional fishmeal and fish oil plants.…